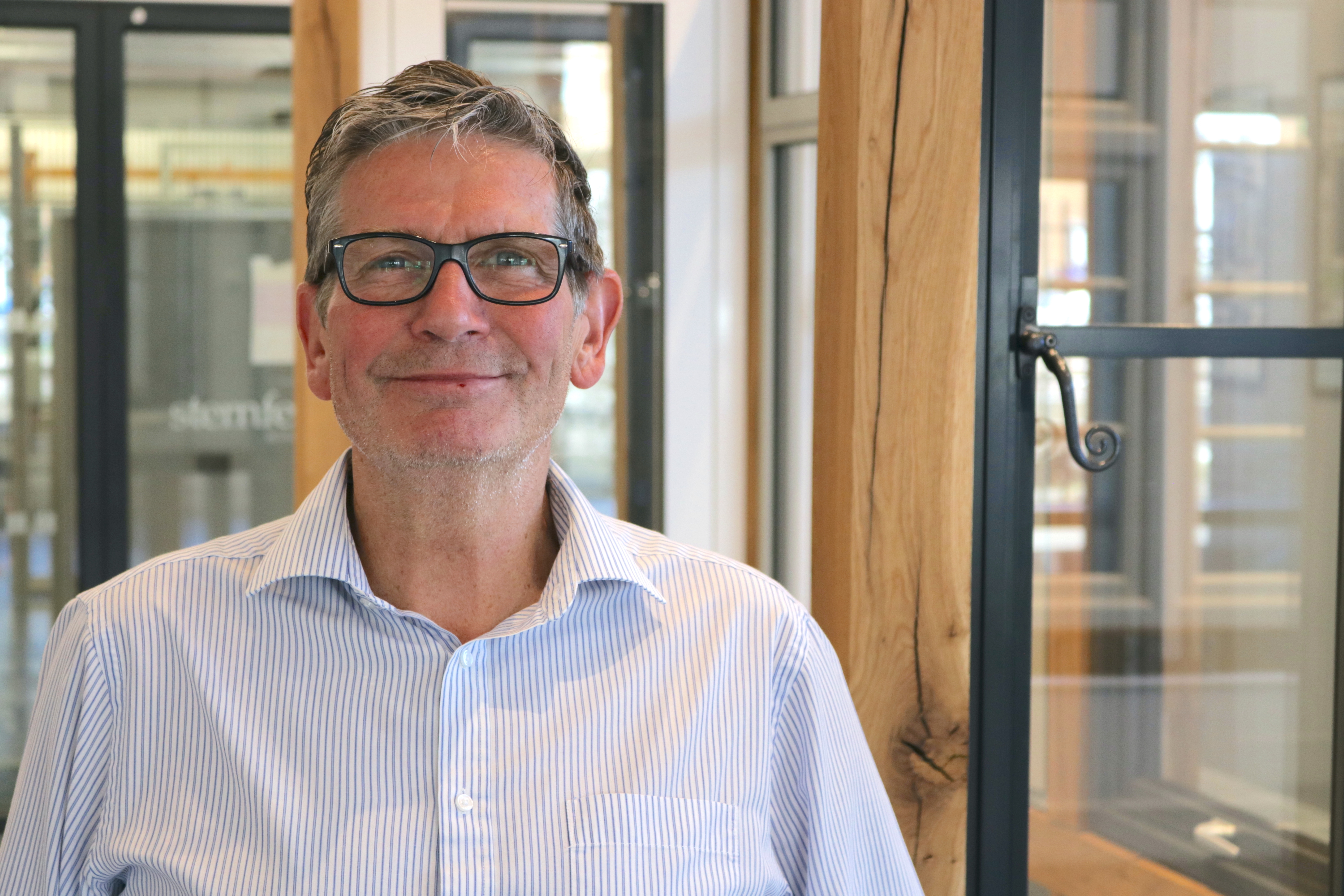
Making The Difference
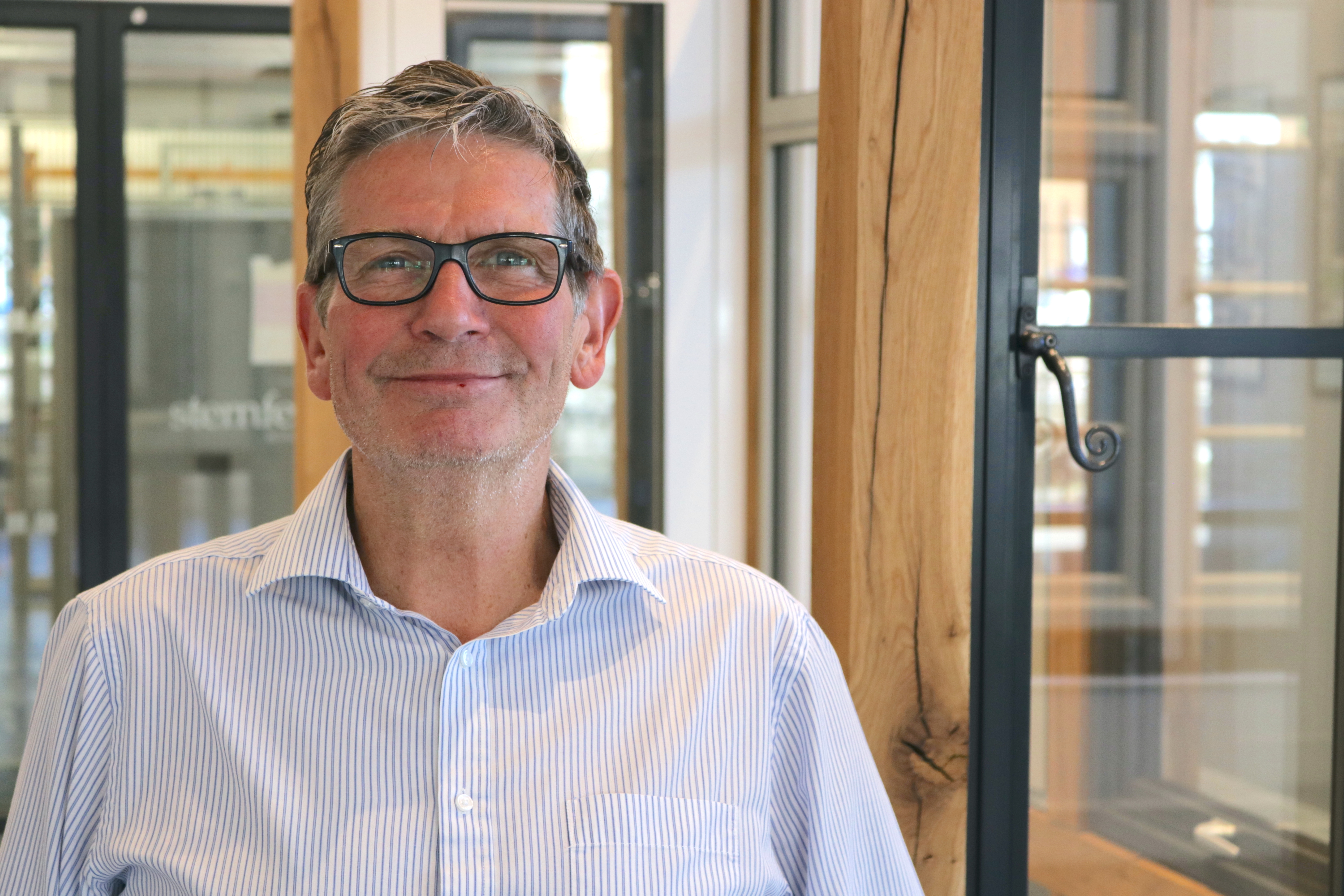
Kev Wallis is Technical Sales Manager for Lincoln based fabricator, Sternfenster, where he has been an integral part of the team for 40 years. Kev works across all areas of Sternfenster’s operations, from customer services to manufacturing, and spends a significant part of his day working side-by-side with customers to solve technical and training issues.
In my previous columns, I’ve explained how even the most experienced fitters can still make silly mistakes and how a lot of problems could be solved if installers were prepared to occasionally swallow their pride and read a manual.
I’ve also highlighted that Sternfenster has produced a comprehensive library of training videos, that can be viewed on YouTube or downloaded from Sternfenster Plus, that show how to correctly fit all of our products.
For my third and final column for Total Installer, I’ve revealed four more areas that have the potential to make the difference between a successful installation or an embarrassing and costly call back.
Don’t be foiled by the weather
We all know that foils and coloured products are becoming much more popular these days, which is great – but they do have the potential to create issues for fitters.
Foils, from cream right through to black, really hold the heat compared to good old white PVC and if you’re installing on a hot day, or in direct sunlight, then it’s important to remember that the door will contract once it has cooled.
It might only be a very small amount, but if you haven’t made allowances for this when making final adjustments on the door, you may very well get a call back from an unhappy customer when the sun goes down.
This could be because the door is grating or grinding and generally just doesn’t feel like it’s working properly, but the worst-case scenario is that it will have moved so much it no longer locks. And you don’t want to be dealing with a homeowner that’s been up all night long stressing about an unsecured door!
Location, location, location
Coastal properties may provide fantastic views for those lucky enough to live in them, but they have the potential to cause headaches for installers – purely because of the notoriously bad coastal weather in the UK!
If you’re installing in a location that’s likely to have more extreme weather or environmental conditions, then it’s good practice to let your supplier know before you order your products. It might be the case that they can recommend a more robust specification for certain components.
For instance, we have a customer in Folkestone who, as a matter of course, specifies extra drainage to cope with the rain that blows in off the sea and drip rails on his tilt and turns. Another, based inBognor, always specifies stainless steel screws, just to be on the safe side.
Pay attention to the chevrons
Most of our products are assembled in the factory and are delivered to site ready to fit, but in some instances they are supplied flat packed. If this is the case, then you need to pay extra special attention to the chevrons that are designed to hold the frame together at 90 degrees.
In the past, I’ve been called out to site for bi-folds that are said to be not working properly and I’ve spotted straight away that the joint has slipped on the outer frame. You can see it in the 45 degree mitre joints.
The key thing to remember here is – once again – read the manual! Our flat pack doors are made up in the factory, tested prior to despatch and then delivered with all the parts you need for assembly.
Everything is there, from the screws to the chevrons, so the only way you can really mess it up is if you don’t follow the instructions.
It’s a two-man job
Or at least it is if you’re fitting an oversized door, patio or bi-fold that has really big glass units. In the same way that we have seen more and more demand for colour and foils, we’ve also seen a rise in big bi-folds and sliding doors as homeowners want as much glass as they can possibly get.
There are strict rules when it comes to the weight of products and if there is only one person on site when our lorry arrives – and the sticker on the glass unit says it needs two to lift it – the driver will not deliver it. It’s as simple as that.
On the plus side, there is very little excuse to miss a delivery from Sternfenster! We provide 2-hour delivery slots and our drivers will typically call to provide an update when they are around 30-mins away.